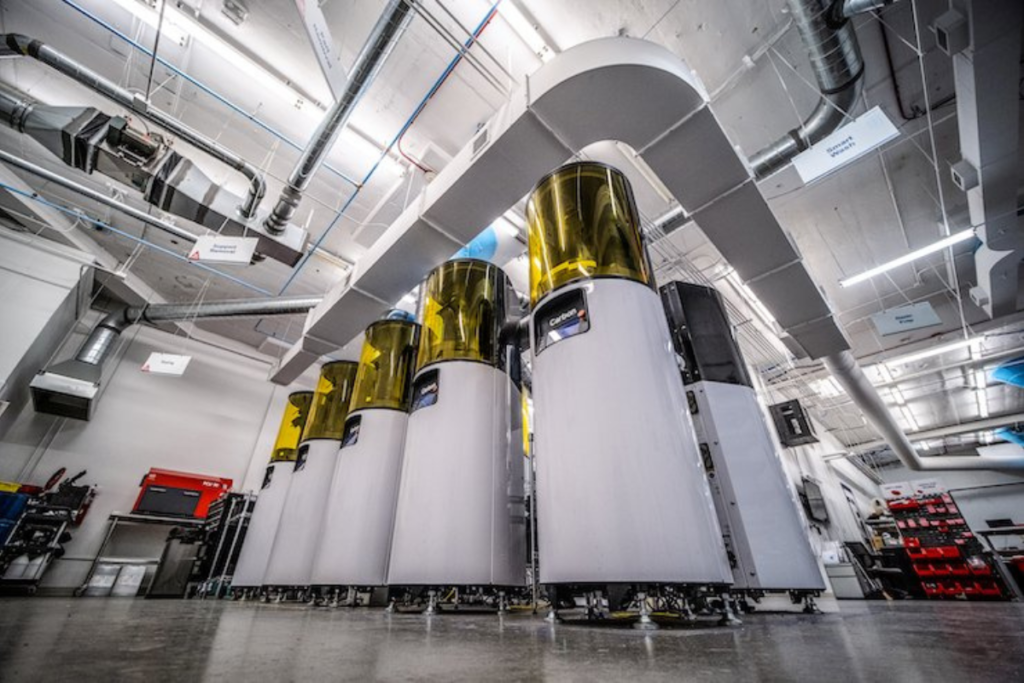
3D printing, also known as additive manufacturing, has revolutionized the manufacturing industry. Initially, it was used for prototyping; however, it has since evolved to be a valuable tool for mass production. This article will explore the advantages of 3D printing for mass production, its various applications, and the materials used for 3D printing.
Advantages of Using 3D Printing for Mass Production
One of the major advantages of 3D printing for mass production is that it significantly reduces the time-to-market. In today’s highly competitive market, it is crucial to bring a product to the market quickly. The use of 3D printing in rapid prototyping allows manufacturers to produce functional prototypes for testing and development. The technology also allows for rapid tooling, which can be used to create 3D printed injection molds for mass production.
Another advantage of 3D printing is its flexibility in manufacturing. Manufacturers can quickly modify designs if errors are detected, making it a great tool for batch production. The ability to customize products is also an advantage of 3D printing. With 3D printing, it is easy to customize products according to orders, and different materials can be used to achieve this.
Applications of 3D Printing for Mass Production
3D printing can be used for various applications in mass production. For example, the technology can be used to manufacture automotive parts, aerospace components, and medical implants. 3D printing is also used in the production of consumer products such as toys, household fixtures, jewelry, and vases.
In the automotive industry, 3D printing is used for the production of lightweight and complex parts. It is also used to create prototypes for testing and development. In the aerospace industry, 3D printing is used for the production of complex components and parts with intricate geometries that are difficult to achieve with traditional manufacturing methods. 3D printing is also used in the medical industry to manufacture implants, prosthetics, and other medical devices.
Materials Used for 3D Printing
Several materials can be used for 3D printing, and they are categorized into plastics, resins, and metals.
Plastic polymers are the most commonly used materials for 3D printing. They are known for their strength, flexibility, smoothness, and color options. Polylactic acid (PLA) is a popular eco-friendly plastic made from natural products and known for its biodegradability. Acrylonitrile butadiene styrene (ABS) is another plastic polymer known for its strength, firmness, and flexibility. Polycarbonate (PC) is a plastic polymer suitable for making electrical and telecommunication products. Polyamide or Nylon is a popular 3D printing material because of its strength, flexibility, and high level of detail.
Resins are less commonly used materials for 3D printing. They reach their end state when exposed to UV light and have different color options. High detail resin is used for intricate models, paintable resin is suitable for models with rendered facial details, while transparent resin is suitable for models that must have a smooth surface and transparent appearance.
Metals are the second most popular 3D printing materials. They are used through direct metal laser sintering (DMLS) and are suitable for the production of aerospace components, medical implants, and other high-performance parts.
Takeaway
Over the past few years, 3D printing has transformed the manufacturing industry, and its applications have been expanding rapidly. Its ability to produce complex structures and components with ease, speed, and accuracy has revolutionized traditional manufacturing processes, making it an attractive option for mass production.
The advantages of 3D printing in mass production are numerous, including the ability to rapidly produce high-quality prototypes, the flexibility to make design changes quickly, and the ability to customize products to meet specific needs. These advantages have made it an increasingly popular choice for manufacturers across various industries.
One of the most significant benefits of 3D printing is its ability to produce parts and components that are difficult or impossible to create using traditional manufacturing methods. With 3D printing, manufacturers can produce complex and intricate designs with ease, making it an ideal tool for industries like aerospace and automotive.
Moreover, the use of 3D printing in the medical industry has opened up new possibilities for the production of customized medical implants and prosthetics, making it easier and faster to produce highly personalized products tailored to individual patients’ needs.
As new materials and technologies are developed, the potential applications of 3D printing are expanding rapidly. The use of advanced materials, such as carbon fiber and metal, has enabled the production of parts and components with greater strength and durability, making it possible to use 3D printing for even more demanding applications.
In conclusion, the rise of 3D printing in mass production has revolutionized the manufacturing industry. Its advantages, such as faster time-to-market, flexibility, and customization, have made it an essential tool for manufacturers in different industries. As the technology continues to evolve, it will be exciting to see how it shapes the future of manufacturing and opens up new possibilities for product design and development.